
Majority of airplane structure made from light weight carbon fiber reinforced plastic (#CFRP).
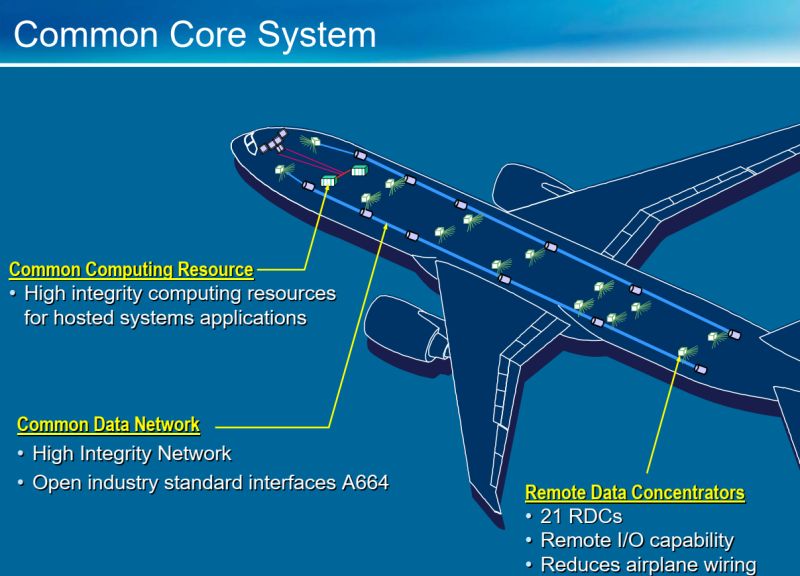
Lower cabin altitude pressurization (6000 ft) due to CFRP strength lower Pressure with higher Humidity gives improved air quality in the cabin, larger flight deck and larger passenger windows.
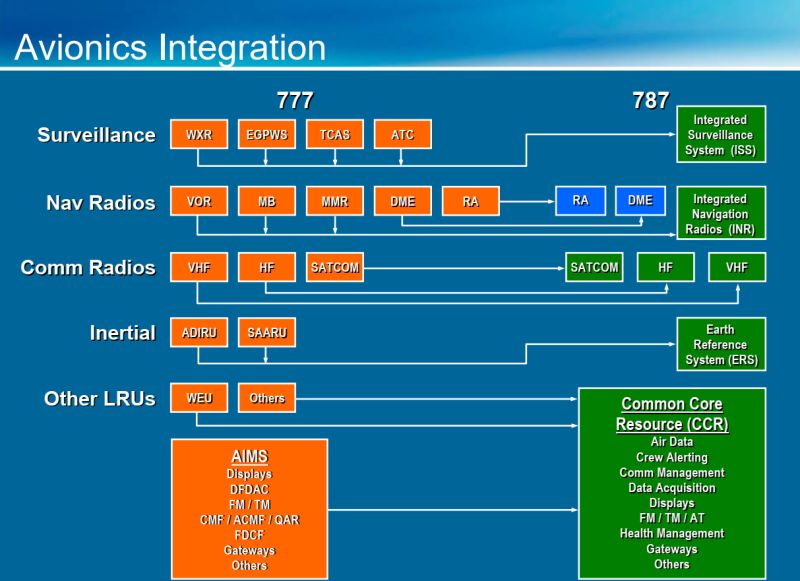
Flight deck with liquid crystal display (LCD) primary display system (PDS). – Common core system (#CCS) with high-speed fiber optic common data network (CDN). The common core system (CCS) has #software applications that do calculations for most, but not all, of the airplane systems.
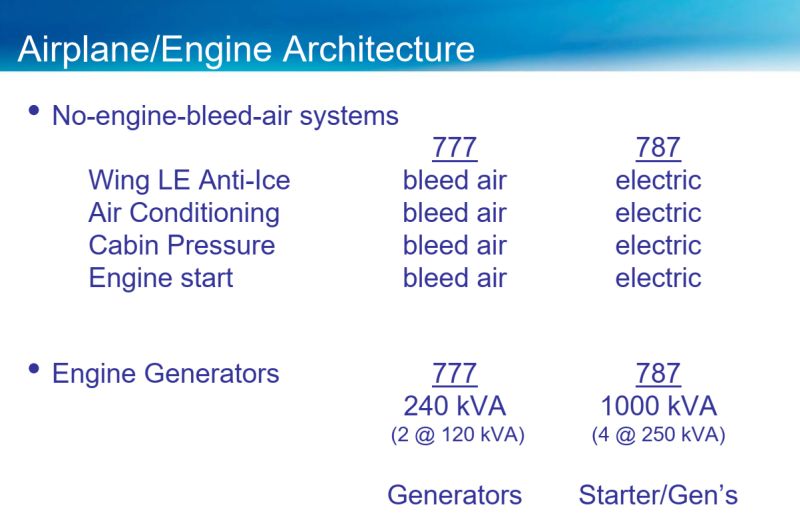
Integrated fully Fly-by-wire flight control electronics (FCE) with Flaperons. – Electric airplane architecture (no engine bleed of pneumatics except engine anti-ice).
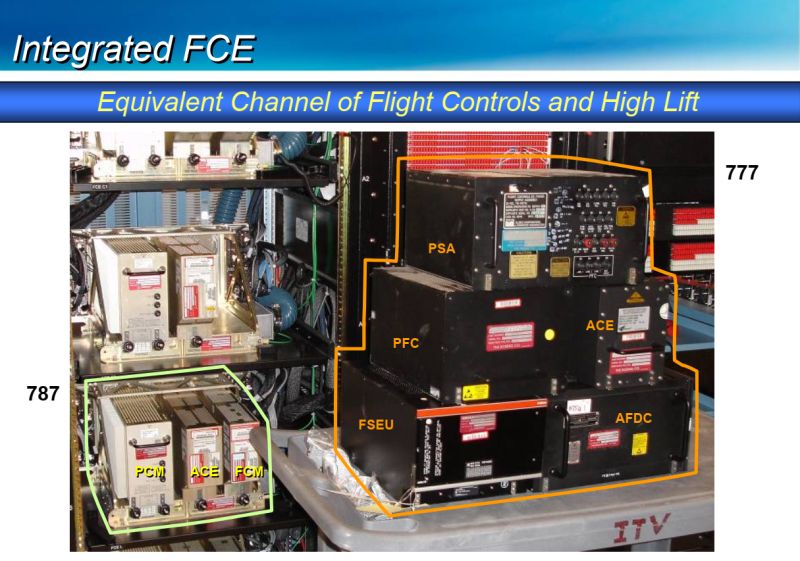
Pneumatic source for air conditioning system is from electric motor cabin air compressors (#CAC).
235 Vac Variable Frequency Power Generation Systems; Two 250 kVA Variable Frequency Starter/Generators (#VFSG) on each engine (this was 120 kVA max in previous Aircrafts), Two 225 kVA (VFSG) on APU. (No constant 400 Hz frequency, Freq range 360-800 Hz). Hybrid AC and DC electrical power system; 115 Vac, 28 Vdc, 235 Vac, ±270 Vdc all are used in the aircraft. – Electrical engine start.
Electrical brake actuator system, Brake-by-wire, steer-by-wire. Wireless Tire Pressure sensors. – Electrically heated wing leading edge anti-ice system.
2 main electronic equipment (EE) bays: Forward EE Bay is below the flight deck and cabin floor, Aft EE Bay is below the cabin floor, forward of the aft cargo compartment.
3 External Power Connection, 2 of them is necessary always for normal operation and the 3. one needed for high load operation like hydraulic pumps, Packs or Engine start.
Current Return Network (CRN) because Carbon Fiber does not lend itself well to current “flow”, there is a need to ‘Earth’ the aircraft for Electrical components and Lightning Strike protection.
Circuit Breaker Indication and Control (#CBIC) system; most of the CB are Electronic CB monitored and controlled by CBIC, with ability to pull, close, tag or lock the CB from the cockpit Multi-Function Display MFD.
Three separate 5000 psi hydraulic systems. Reduce system weight, smaller actuators and tubing, bootstrap Type Reservoir use hydraulic pressure to pressurize the reservoir. No air pressure. – Automatically started APU when three or more engine generators go offline.
Liquid cooling system for Power Electronics.
2 Digital Flight Data Recorder, CVR removed and included in the DFDR system.
Integrated Avionic systems; Ex 1; WXR, TCAS, ATC & EGPWS in one computer ISS (Integrated Surveillance System). Ex 2; VOR, MB, ILS GPS in one unit INR (Integrated Navigation Radios). And many other features and details.
Do not forget, every new design comes with new problems and new troubleshooting methods.
Author – Firas Naser
Licensed A/C Maintenance Engineer B1/B2/C & Part147 Tech. Instructor for A320 CEO CFM56/V2500, A320Neo LEAP-1A, A330-200-300 RR Trent 700/GECF6/PW4000, B737NG, B737MAX LEAP1B, A310/A300-600.