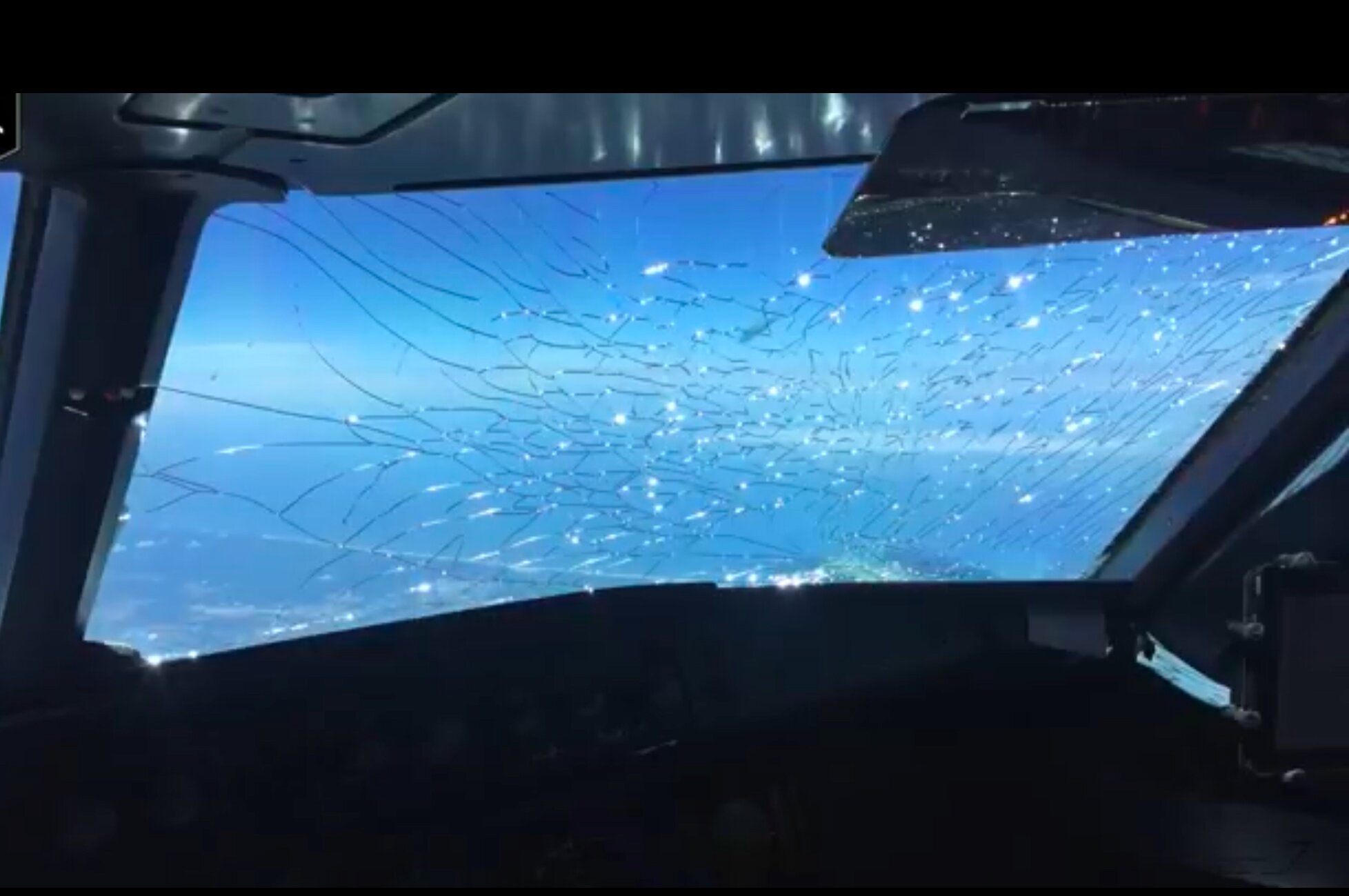
When you’re in flight-deck, the only thing separating pilots from the minus 56 degrees centigrade and unbreathable, thin air outside is an airplane cockpit windshield. On one side, there’s a warm, pressurized cabin where you can work and on the other, a world that would kill you in minutes if you were exposed to it. Between the two, just incredibly sturdy windshield. There are two primary purposes for the windshields. Number one, protect the crew from the outside harsh environment and number two allow the crew to see outside. Besides pressure, temperature control, and bird strike, aircraft windscreen area has to withstand chemical resistance to things like hydraulic fluid or jet fuel as well as abrasion including rust, snow, or rain erosion and the most dangerous the static electrical discharge (saint Elmos fire) / lightening.
“The windshields have to withstand all of that, and sometime more than that too”.
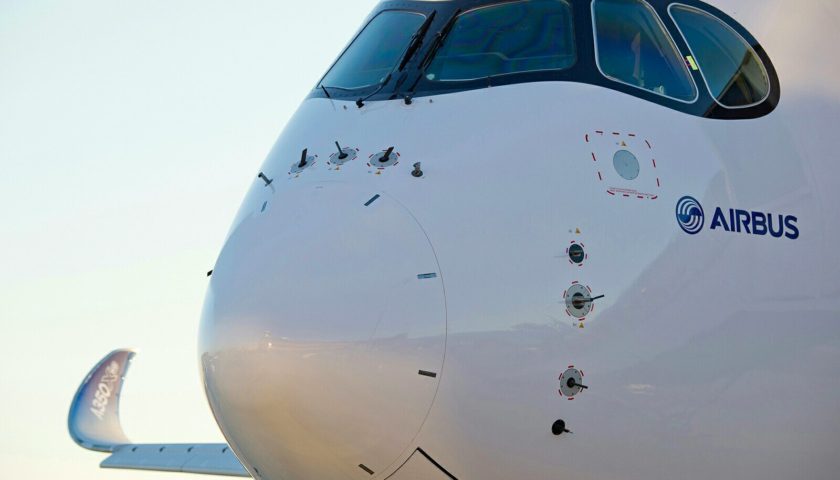
Flight Deck Windshields Design and Material
Aircraft windshields typically comprise a laminated structure consisting of layers of glass, acrylic or polycarbonate plastics, or combinations thereof bonded together by interlayers of polymeric bonding material. This laminated structure provides high strength at reduced weight necessary for use in aircraft. The environment to which such laminated windshields are exposed is severe and the outer surface, known as the face ply, is often damaged due to particulate impacts, scratching or bond failures (delaminations) at inter-layer interfaces and/or electrical faults in anti-icing heater coatings caused by cyclical thermally and mechanically induced stresses, moisture ingress and bond deterioration. Such damage is the chief cause for removal of front windshields, and almost invariably occurs at the inner surface of the outermost ply and/or within the interlayer adjacent thereto. Whether it’s for a short, medium or long-haul aircraft, the range of windscreen thickness is the same. It varies between just under an inch to 1.2 inches. Therefore, a passenger plane windscreen is on average four times thicker than a car windscreen which is 0.23 inch thick. The flight deck windshields are made with glass-faced acrylic — an outer layer of glass bonded to stretched acrylic. Then, there’s a layer between them, made of urethane. Each has anti-ice and anti-fog systems.
Cockpit windshield on the Boeing 787

Cockpit windshield on Airbus 320

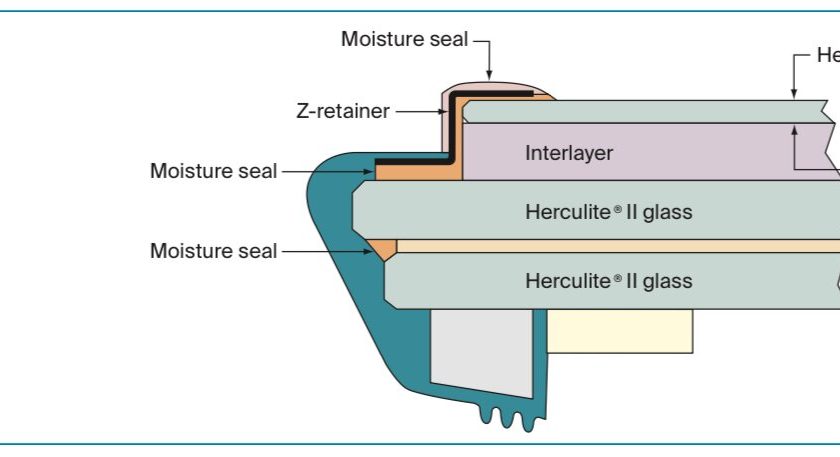
Cockpit windshield on the Boeing 747

In some cases, such as the Boeing 737 and Boeing 747, the windshield features two plies of tempered (i.e. hardened) glass along with an interlayer.
How are the Measurement of individual layers and total thickness in aircraft windshields done?

Multilayer plastic construction is commonly employed by the aerospace industry for air-craft windshields, in which two relatively thick layers of acrylic or a similar hard plastic are typically sandwiched around a thinner layer of a soft material such as polyvinyl butyral (PVB) which provides thermal stress relief. The hard plastic layers are typically about 0.4 in. to 0.5 in. (10 to 12.5 mm) thick and the soft inner layer about 0.050 in. (1.25 mm) thick. Scratches in aircraft windshields are typically removed by polishing during routine maintenance, after which thickness measurement is required to ensure that windshield thickness has not been reduced below a specified minimum. Additionally, manufacturers need to measure the soft PVB middle layer to ensure that it is within a specified thickness. Thickness gauges like 38 DL Plus are used for the above measurement.
Windshield Fasteners
Some aircraft windshields are fastened with bolts. Others use a clamping system, both methods are equally reliable. “The Airbus A320 and A340 are clamped-in design, without bolt holes. Boeing aircraft, on the other hand, are typically bolted-in designs. If you want to make the window an integral part of the aircraft structure, then a bolted in design is the way to go because it transmits the aircraft loads right through the window. The window becomes a structural part of the front of the fuselage. The alternative is to isolate the window from any possible loads being transmitted by the aircraft. What happens then is that you have to have a heavy metal fuselage build-up, or frame, around the window to isolate it. When windows are damaged, they have to be replaced, except in certain cases of very minor damage— light scratches or scuffs—which must be repaired by experts. The typical service life of a flight deck window is ten years, less than half of the rated service life of most aircraft, which is around 25 years.
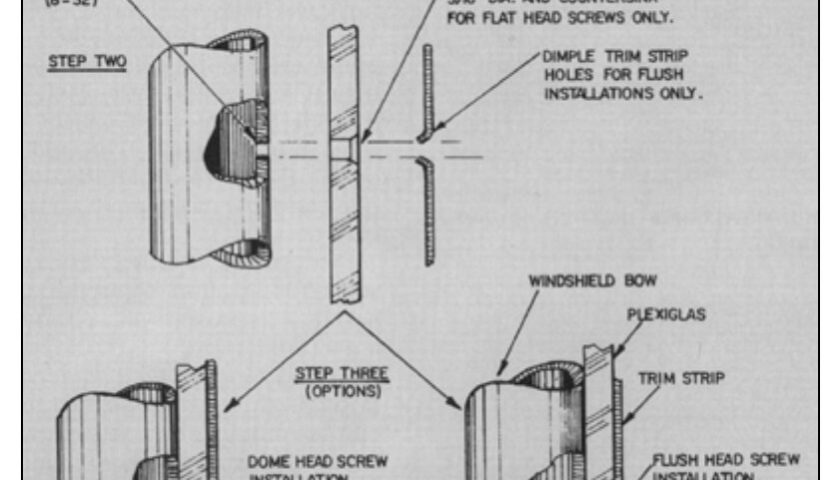
Aircraft Windshield Frost, Fog and Ice Prevention / Protection
On your car, in the back window, you’ll see those lines for defog or defrost, and the air-craft window has something similar. It has a film on the outer glass that is electrically heated.
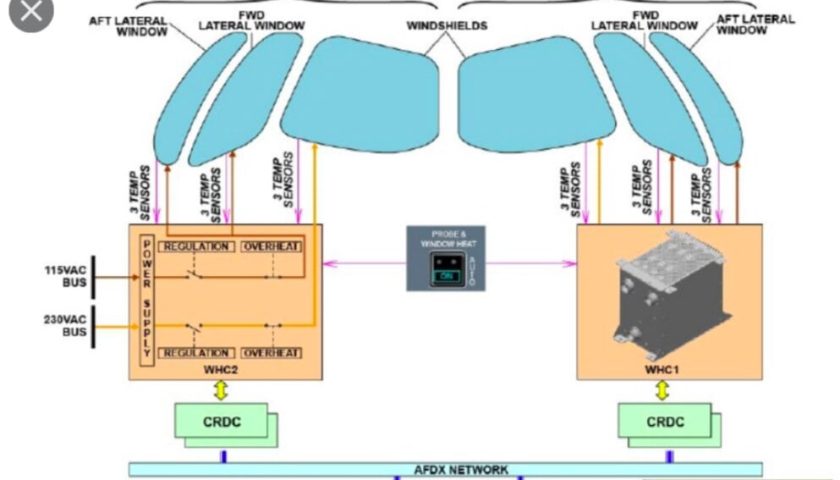
Power goes to the film and the film heats up and deices the window on the outside. Be-sides the wires that heat the window using electricity, there are also sensors to measure resistance and to control the heat—so that the window never becomes too hot or too cool for operating limits. The window heating system makes the necessary adjustments at varying altitudes and in varying weather. Some systems are automatic while others are controlled by cockpit switches. Separate circuits for pilot and co-pilot are common to ensure visibility in case of a malfunction. Windshield anti-icers usually use resistance heat to clear windshield or chemical spray while on the ground. Liquids used include ethylene glycol, propylene glycol, sodium acetate, and chloride salts.
That oily sheen on the windshield?
Have you ever noticed that the cockpit windshields sometimes look like they have oil on them? That oily sheen is actually a coating of indium tin oxide, which is electrically conductive and transmits heat. Just nanometers thick, this coating sits between glass plies and is completely transparent. Accordingly, this thin coating is all that is needed to keep the windows nice and clear in frosty weather. A windshield of an aircraft includes a heater in order to prevent the occurrence of fogging due to a temperature difference and adhesion of ice.
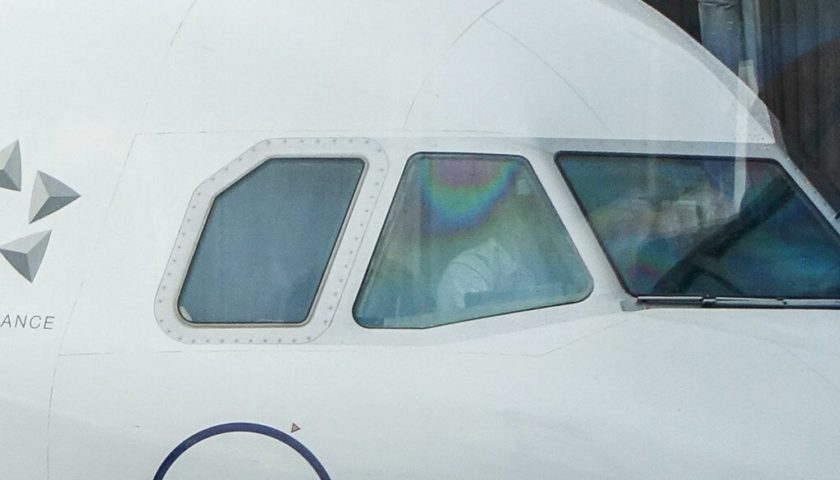
What About Bird Strikes?
Bird strikes have long been a significant threat to aviation safety. The first bird strike is dated back to 07 Sep 1905, recorded by the Wright brothers.
To ensure flight safety, aviation regulations require a certain level of bird strike resistance for critical components. As specified in Federal Aviation Regulations, an airplane must be capable of successfully completing a flight during which likely structural damage occurs as a result of impact with a 4 lb (1 lb = 0.4536 kg) bird (8 lb for an empennage structure) when the velocity of the airplane relative to the bird along the airplane’s flight path is equal to Vc (design cruise speed) at the sea level or 0.85Vc at 8000 ft (1 ft = 0.3048 m), whichever is more. ( Vc equal to around 340 knots indicated approx)
Soft bodies such as fowls and gelatin are used by the aircraft industry as substitute bird impactors, which have physical properties closest to those of living birds, and are observed to flow over a structure during impact, spreading the load over a significant surface area which limits local impact damage.

In-flight cracking
The most common problem that airlines have with flight deck windows is in-flight cracking of the outer ply. Conditions that lead to cracking begin with moisture around the aerodynamic seal (also referred to as the aero seal, moisture seal, or hump seal). Moisture ingress eventually causes delamination, heat-coating problems, and arcing, which — if not corrected — lead to cracking of the outer ply. The aerodynamic seal around the perimeter of a window is subject to erosion by wind and rain. Maintaining the aerodynamic seal in good condition is critical in preventing erosion and moisture ingress and improving the windshield service life.
During flight, cockpit windows may be damaged due to:
(a) Impact with foreign object
(b) Electrical arcing of the windows heating system
(c) Natural ageing of the heating film
(d) Moisture ingress
(e) Delamination
(f) Manufacturing quality defect
(g) Damage during installation. In the case of a cockpit windshield/window cracking, the flight crew should carefully evaluate the damage.
A heating film cracking A heating film cracking looks like roughly a straight line across the window starting from a window edge. In most of the cases the line stops in the middle of the window.

An outer ply cracking An outer ply cracking usually shows a few broken lines that start from one edge of the windshield or from a foreign object impact, and go through the window to another edge.
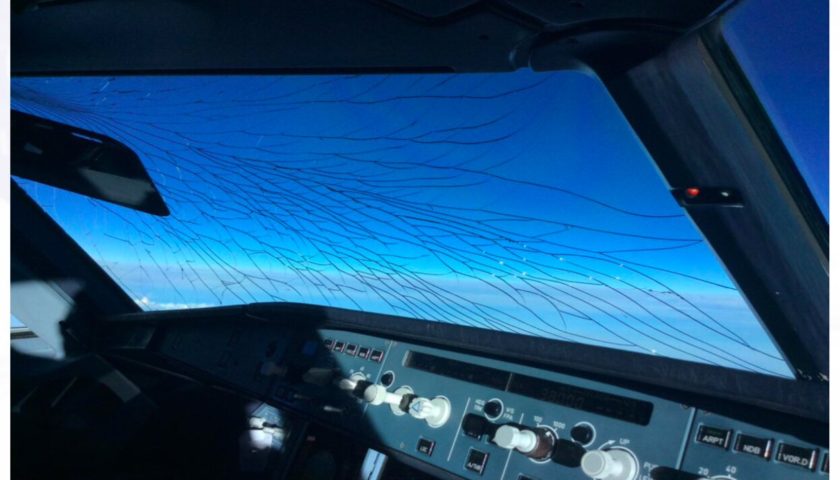
Inner ply or Middle ply cracking A structural ply cracking (Inner ply or Middle ply) has a break pattern that covers the entire surface of the windshield. The small pieces of broken glass impair the visibility.
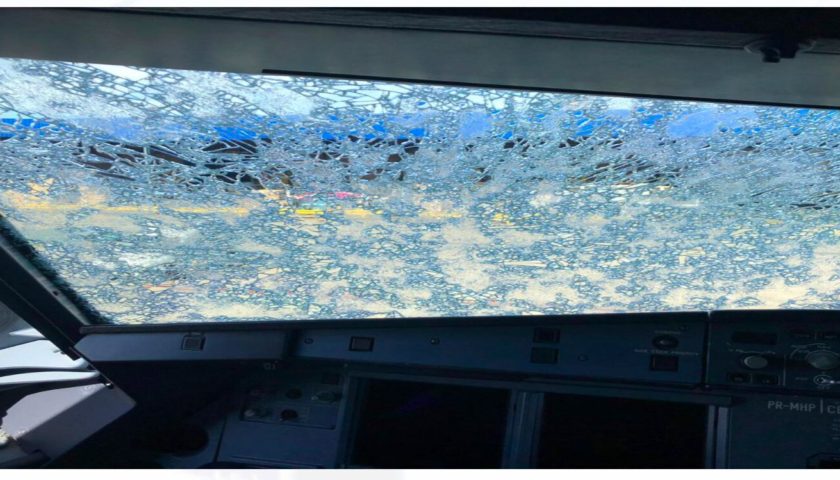
Windshield crack Identification and procedures
If a crack appears, determine if it is on the inside or outside panel of glass. If it is determined to be the outside panel continue the flight but write it up. In case of windshield damage/crack due to the impact of a foreign object or electrical arcing of the window heating system, the visual clues are not sufficient to assess the structural integrity of the windshield. The flight crew must do a physical check of the Inner ply of the windshield as re-quired by the cockpit windshield/ window cracked procedure in the QRH/ FCOM / Ops manual and apply the procedure accordingly. Touch the crack with a pen or with fingernail:
(a) If no crack on the cockpit side – structural integrity not affected. Generally No limitations. The inner pane is still strong enough to maintain differential pressure up to the maximum flight level more or less meaning fly to your destination airport. The pilot flying should be on the nondamaged side of the windshield.
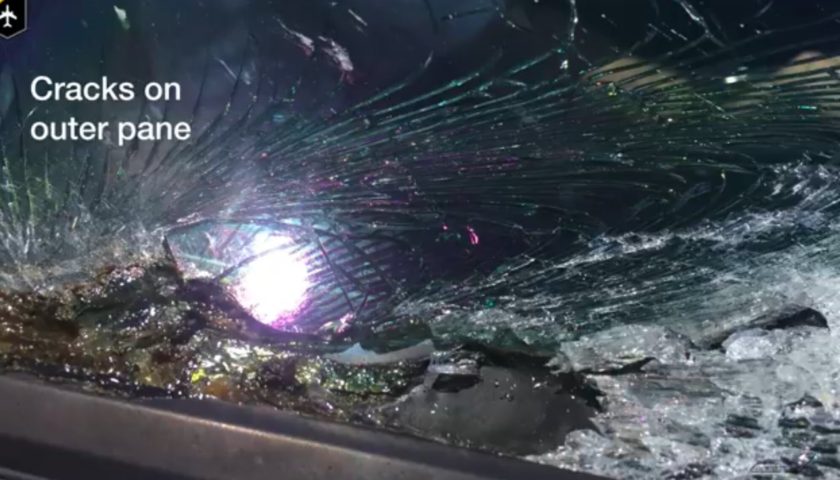
(b) If the crack on the cockpit side – structural integrity may be altered. Generally, limitations on cabin altitude, Differential pressure, flight level, and speed as given in the operations manual will apply. The pilot will initiate the descent to 23000 ft or below to reduce the differential pressure between the cockpit and the outside air pressure down to 5 psi to reduce the risk of further damage which could lead to cabin depressurization. It is recommended to find the next suitable airport to land because at lower levels the fuel flow is significantly higher and unexpected turbulence could damage the windshield even more.
(c) Both windshields damaged: In the case of both windshields are damaged and the visibility is severely reduced. Consider an auto land landing at the next suitable airport. In case auto land is not available and the visibility is so severely reduced on both windows. The pilot flying shall open the side window to get a better view of the runway for the visual approach.
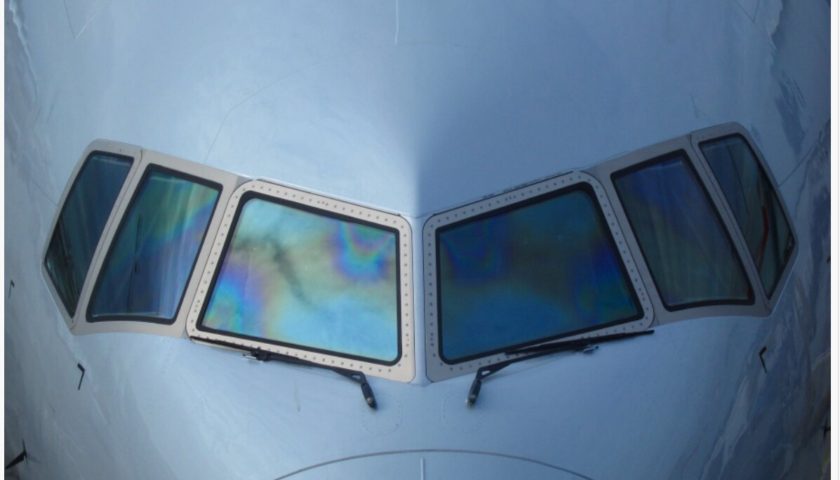
General Points:
(1) Two aspects of windshield geometry are of particular importance in terms of their effects on pilot vision. These are the angle of incidence and radius of curvature. Windshields may be either flat or curved panels or a combination of these. A high angle of incidence and use of curvature is generally desirable for aerodynamic reasons to achieve minimum disturbance of the airflow along the fuselage.
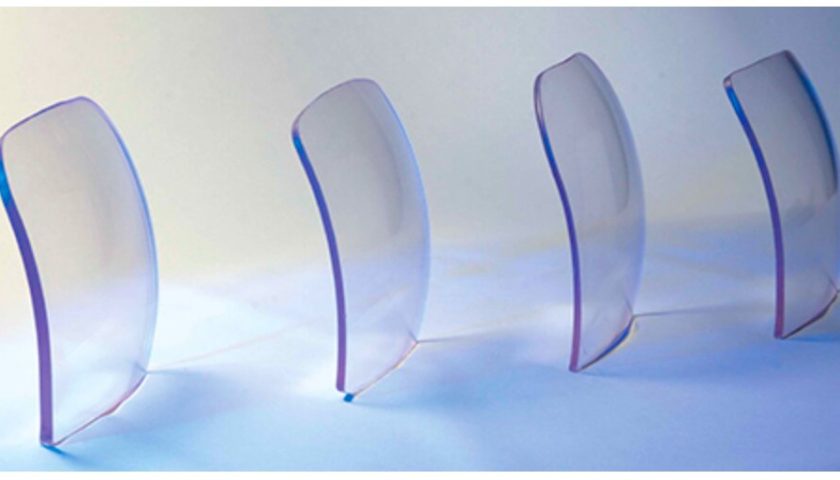
(2) One of the world’s oldest manufacturers of aerospace transparencies (windows) is PPG Aerospace Industries, headquartered in Pittsburgh, Pennsylvania, and Pilkington Aerospace or Sierracin/Sylmar aerospace, California.
(3) Flight deck windshields have in-service life of about 20,000 to 30,000 flight-hours (8– 11 years).
(4) All six windows of airline aircraft roughly cost 100000 USD.
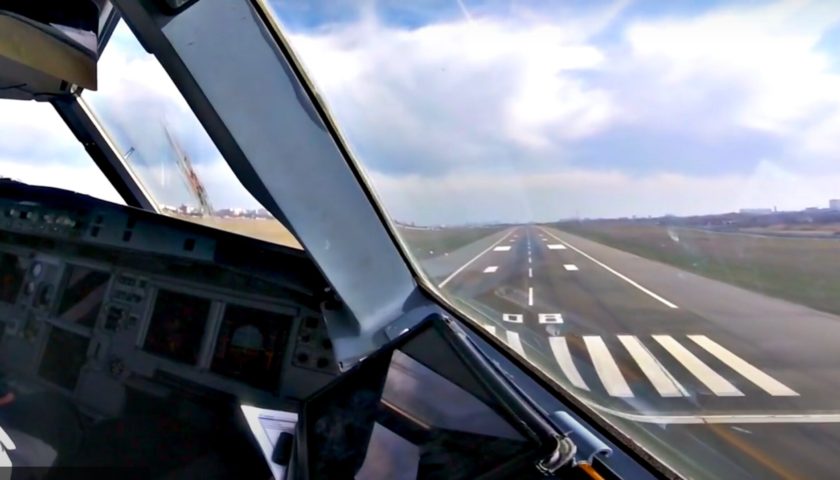
Article by – Anil Goyal