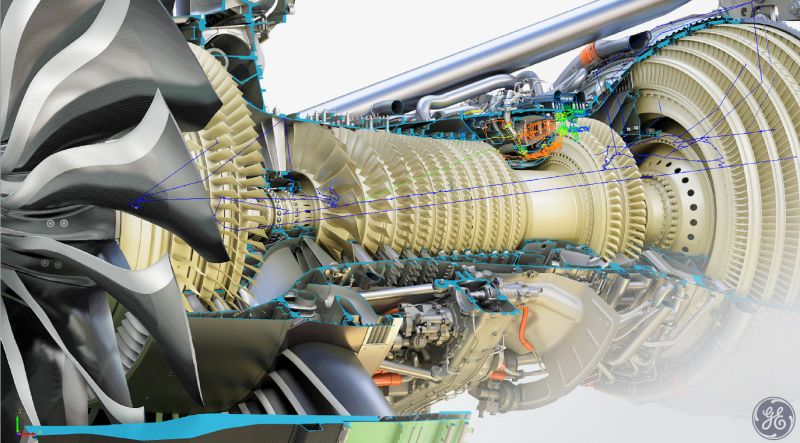
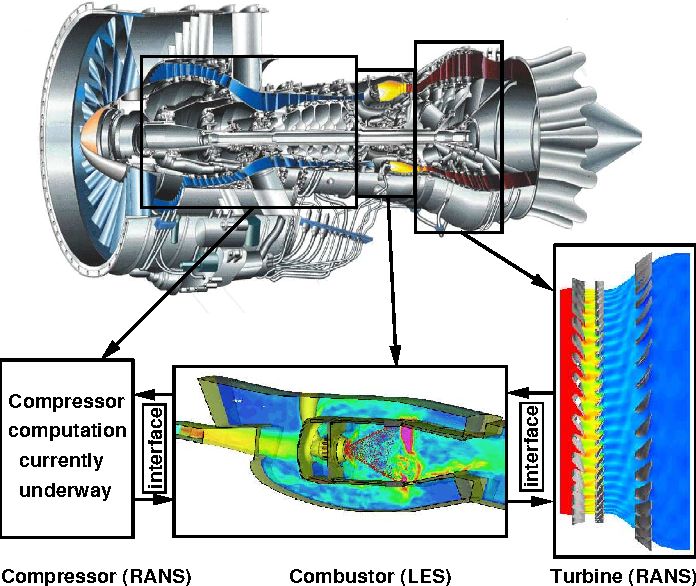
How does Engine Flow simulators work ? How are they promising smart engines with cutting edge technology for power hungry Airframers ?
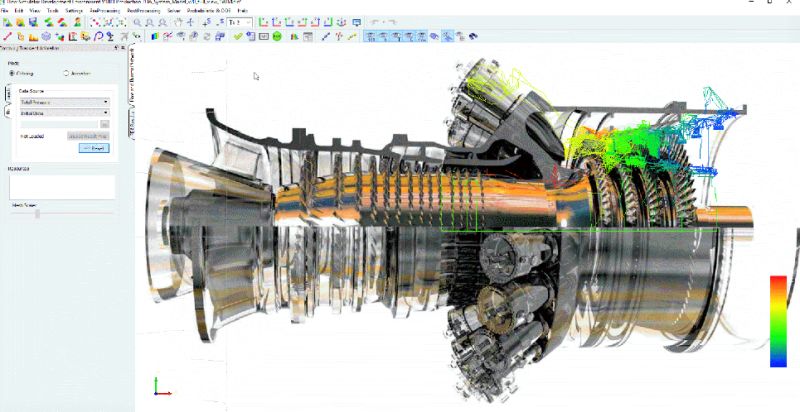
✔Wind tunnels used to be just fine for airframes, engine flow simulation used to struggle, but with advent of Computational fluid dynamics (CFD), both found a mirror to keep their attributes under check.
✔Engine Flow Simulator is an integrated flow, heat transfer,& combustion design software that enables a wide range of simulations to optimize machine & system designs.
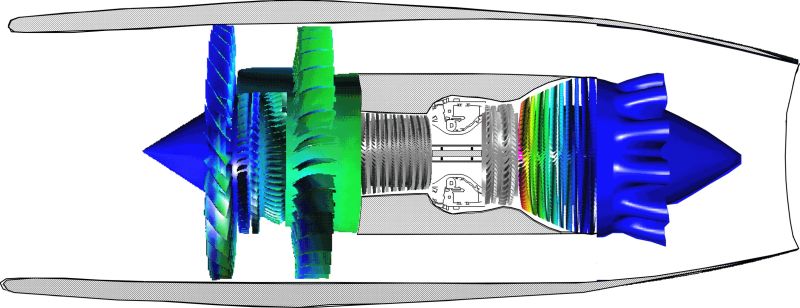
✔To assist engineers in design & problem-solving tasks, flow simulator provides engine interdisciplinary modeling & optimization capabilities within a single platform for machine design in relation to fluid dynamics/thermal/combustion domains.
✔Preconfigured elements/components can simulate a wide range of physical functions including buoyancy-driven flow, compressible/incompressible fluid flow, rotating cavity system flow, radiation/conduction/convection heat transfer & combustion equilibrium-chemistry.
✔Several analysis modes such as steady state, quasi steady state, & transient analysis for fluid dynamics, thermal,& combustions can be simulated to predict system/subsystem run conditions during an engine cycle.
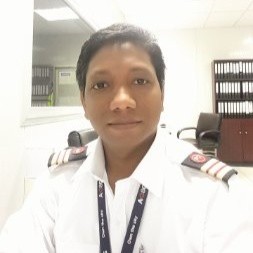
Author – Tanmay Palei
Sr. Aircraft Structure Engineer